Increased tool life and improved cutting parameters
The innovative Family of Silmax 4S treatments for the conditioning of cutting surfaces and rounding of cutting edges, represents another advantageous proposal offered by Silmax.The 4S treatments applied to a tool extend its lifespan and increase its cutting parameters.


Surfaces
The grade of surface finish represents an important element in the manufacturing of end mills and drills and, in general, of all cutting tools. The better the quality of surfaces, the better the quality of a cutting edge, making the following treatment processes even more effective.
A high quality of surfaces is achieved by a continuous improvement of production processes, adopting grindstones of a more and more reduced grain size, balancing the grindstone pack, optimising cutting parameters, as well as by the using of state-of-the-art CNC machines and the choosing of the best machining strategy.
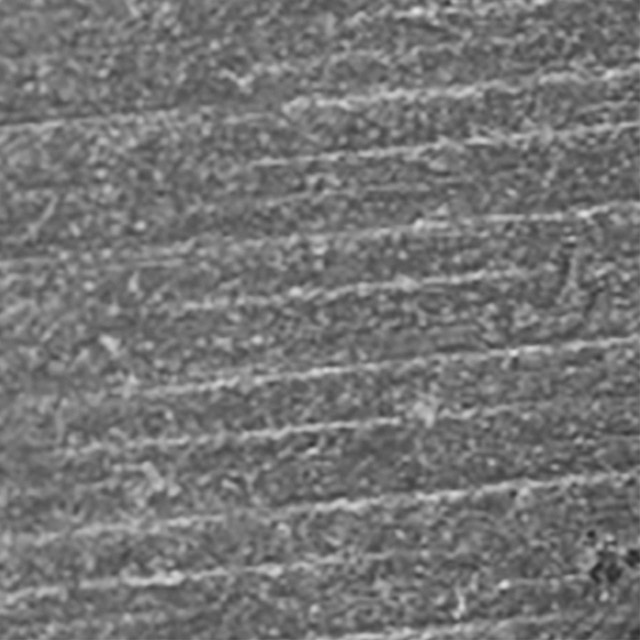
A. Surfaces
Improvement in surface quality
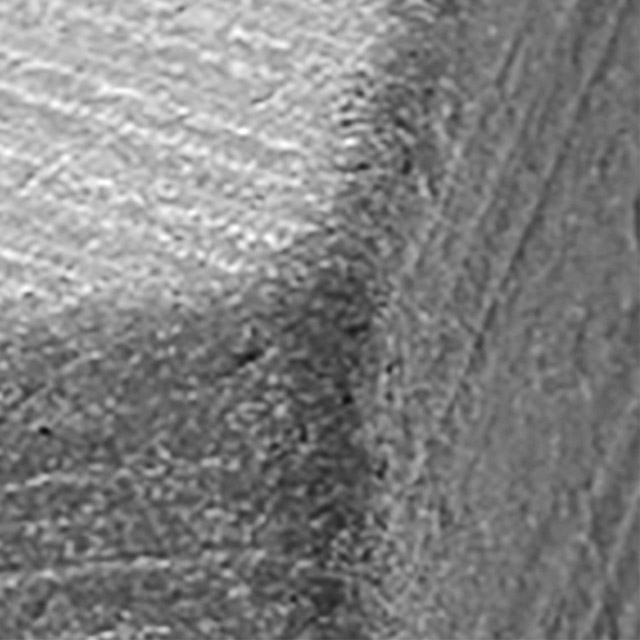
B. Homogeneity
Improvement in cutting edge homogeneity
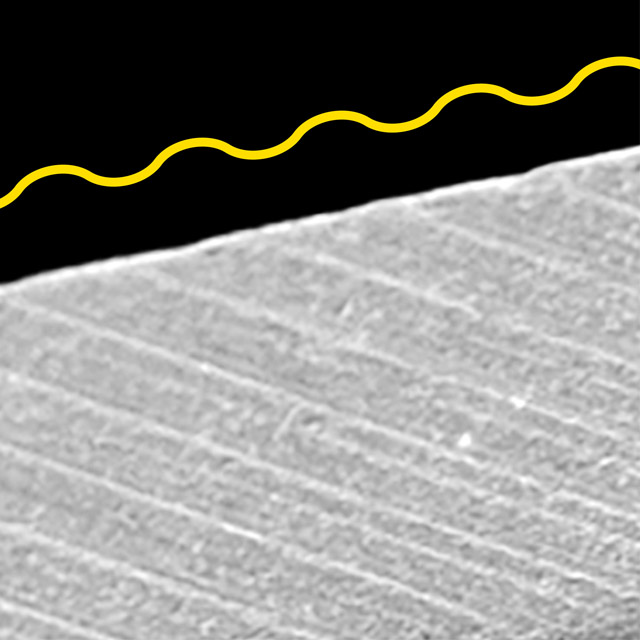
C. Adhesion
Improved adhesion and coating resistance
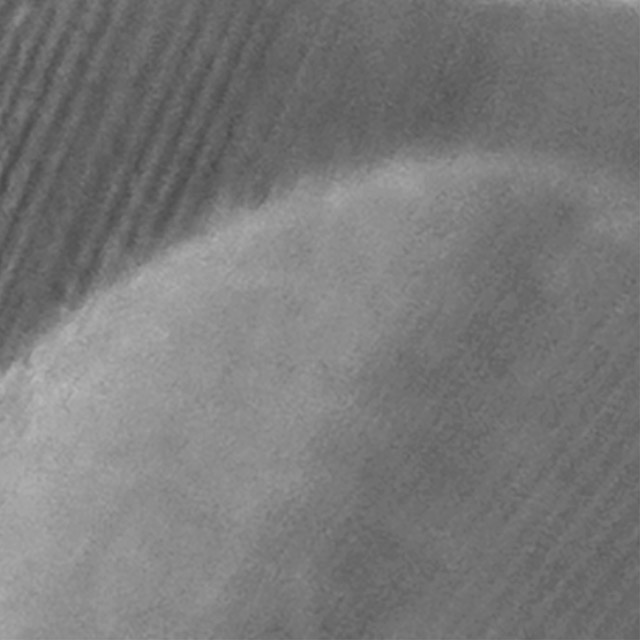
D. Smoothness
Improvement in surface smoothness
Sharp Edge
The rounding of the cutting edge, also defined as honing allows to make the micro-geometry of the sharp edge more homogeneous, while at the same time eliminating micro defects deriving from the sharpening process.
Such defects represent potential points with increased probability of triggering cracks and negatively affect the crystal growth process of the PVD coating.A perfectly homogeneous cutting edge guarantees an extended lifespan of the tool, a better substrate for PVD coating and an improved repeatability of supply over time.



Honing – Form 1
Honing – Form 2
Honing – Form 3
Honing – Form 4
By adjusting the parameters of the honing processes, it is possible to determine the value of the required rounding and its shape according to the result to be achieved.


Coating
The rounding of the cutting edge improves the coating adhesion, while avoiding the “drop” effect due to a sharp and irregular edge.
The coating applied to a tool after honing the cutting edge has a uniform thickness over the whole section, a better adhesion to the substrate and a higher-quality crystalline structure.


“Drop” effect
The PVD coating process displays very small drops of material in the deposited layer, which, after evaporating, aggregates in non-atomic form, then generating the so-called droplets.
The droplets do not affect the properties of the coating, but they cause a higher friction between the cutting edge and the chip being formed, with related phenomena. The treatment processes of the coating aim at eliminating the droplets, thus reducing the roughness of coated surfaces and offering a significant reduction of friction.
Technologies used for 4S treatment
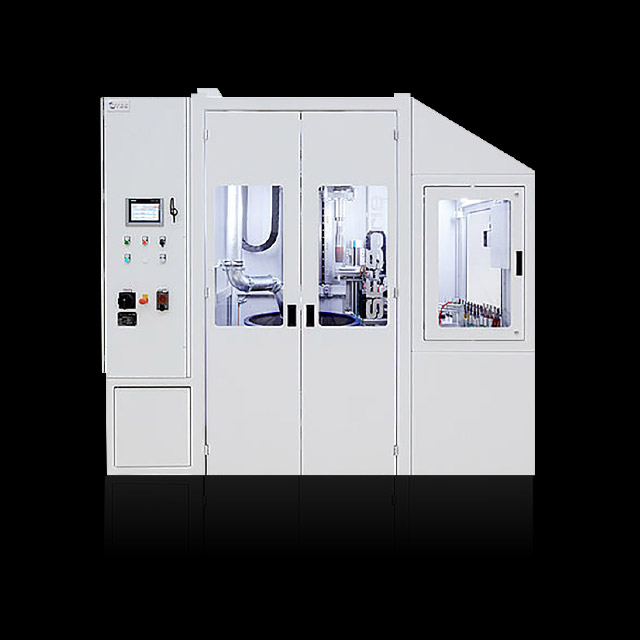
Abrasive-Flow Finishing
The SF technology, also called “abrasive-flow finishing “, has enabled the creation of a new generation of machines for tool honing and polishing. The SF technology ensures an accurate machining with the utmost process repeatability. The PulsFinish®, technology, an OTEC patent, is based on precisely defined movement intervals between abrasive media and workpieces in quick succession, to offer a further improved quality of finish.
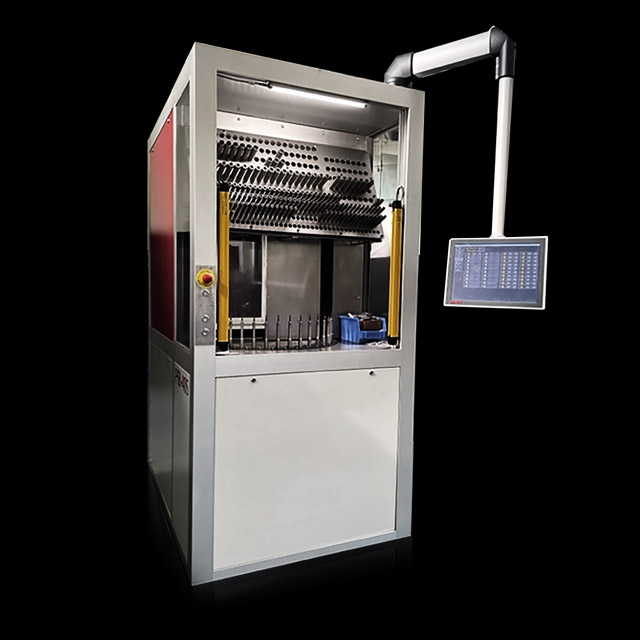
CNC Brush Finishing
CNC brush finishing plants represent the latest technology in automated brush finishing processes.The 4-axis CNC control system allows to parameterise the movement and the rotation speed of the brush, the applied pressure and all the work parameters in an accurate way in every stage of the process.
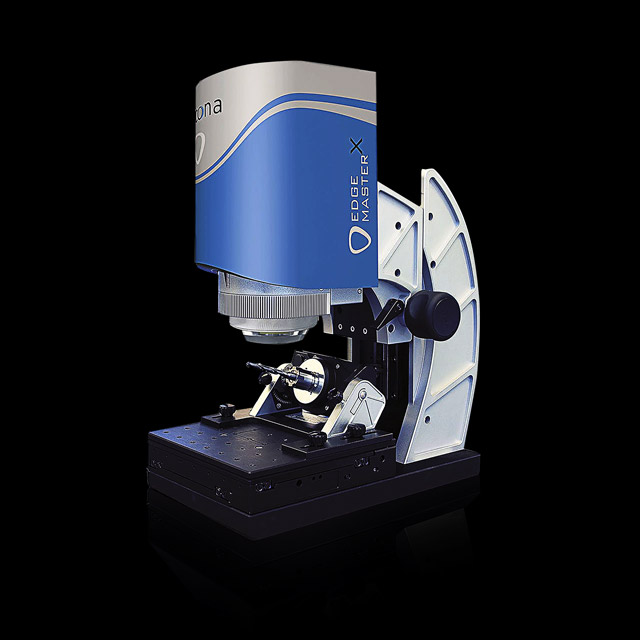
3D Optical Metrology for Edge Measurement
Alicona EdgeMaster is an optical 3D system for the automatic measurement of cutting edges. It represents a product of absolute excellence in the field of 3D optical metrology.The system enables to measure the rounding radius of a cutting edge with extreme precision, to evaluate the roughness of cutting surfaces and to monitor tool wea
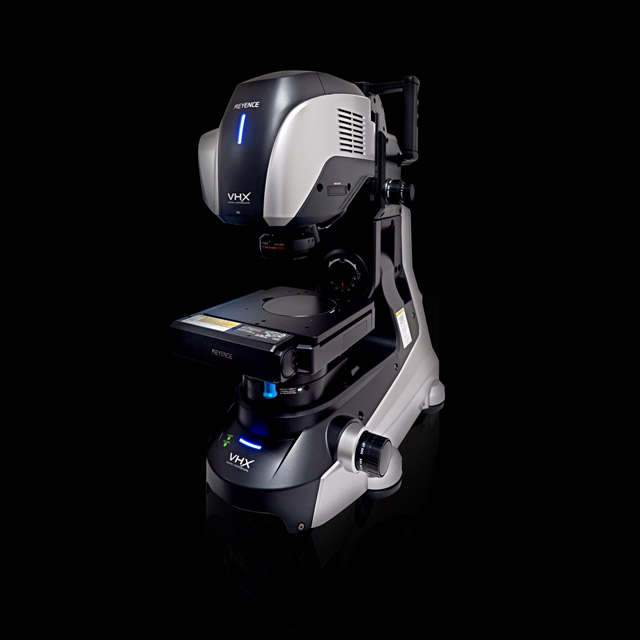
3D Optical Metrology –3D 4K Stereo Microscope
The adoption of a modern, motorised stereo microscope for two- and three-dimensional measurement with 4K resolution and 20X-2500X magnification range allows accurate analyses of surfaces.The instruments for 2D visualisation, 3D profile measurement and surface roughness analysis significantly increase the tribological analysis capacities.